Download a Printable PDF here.
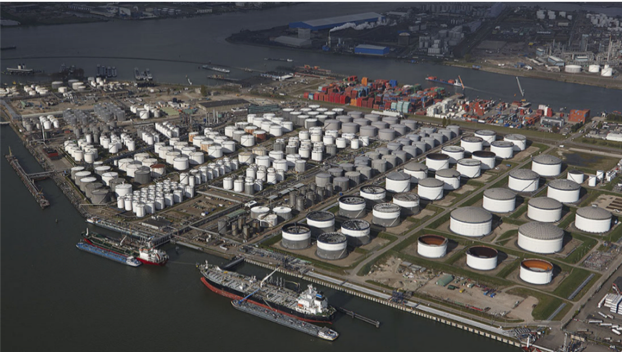
Does your business utilize third-party product storage services? How do you perform your due diligence to ensure your third-party storage terminal handles your product(s) with the same care you do? Have you experienced product quality issues due to mismanagement – for example, inadvertent mixing due to valve misalignment? Have you experienced business interruption and financial loss due to incidents at your storage terminal, even when your product wasn’t involved in the incident? This document presents a risk assessment process specifically tailored for evaluating the sustainability of storage terminal operations.
Many, but not all, storage terminals participate in the triennial survey conducted by the European Chemical Industry Council’s Chemical Distribution Institute report (CDI-T) specific for Terminals. This survey is conducted on-site at the storage terminal by one experienced assessor. The survey is documented in an Excel-based spreadsheet that contains thousands of questions (see the selection in Figure 1), which terminal staff responds to with either “Y” or “N” and in some cases, provide clarifying comments. For most managers tasked with evaluating the risk posed by utilizing the storage terminal, this survey provides limited benefit and often proves to be unwieldy and confusing. There is no easy way to use the survey results to make a good due diligence decision on whether the risk of using the terminal outweighs the benefit. Unless additional resources are dedicated to auditing, there is no other insight into the terminal’s sustainability.
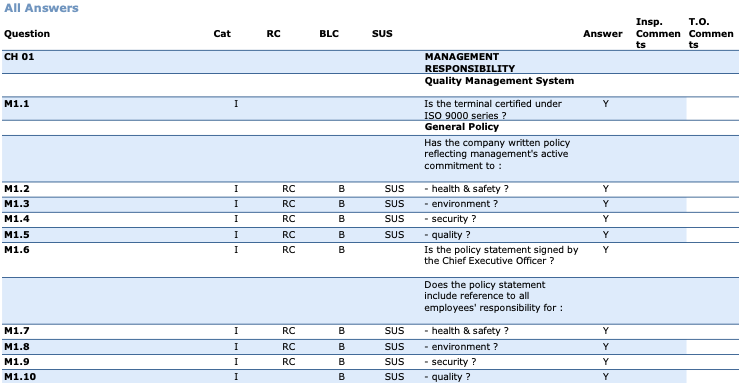
TKC was contacted by a chemical manufacturing client to assist them with evaluating the results of the CDI-T report. The client wanted to then use this evaluation to determine if a terminal should be audited, and if so, utilize the evaluation to focus the audit, thereby reducing on-site time and cost.TKC developed a Facility Risk Assessment Tool tailored to conducting a technical evaluation of the CDI-T report. The tool defines and utilizes the four (4) following dimensions to provide an objective perspective of the CDI-T responses.
- Inherent Risk – the natural risk of the process prior to any safeguards, for example storing large quantities of flammable liquids under any circumstance introduces hazards;
- Dynamic Risk – the risk involved with interacting with the hazard, for example conducting hot work activities in proximity to stored flammable liquids;
- Management Systems – the collection of safeguards, programs, policies and practices targeted at preventing and mitigating hazardous consequences; and
- Performance – an evaluation of the success of the management system.
The tool evaluates each of the fifteen (15) CDI-T report categories, listed below:
- Management Responsibilities
- Quality Management System
- Customer
- Operations
- Non-Conformity Reporting
- Administration
- Occupational Health
- Security
- Training
- Supplier of Goods and Services
- Personnel
- Maintenance
- Emergency Preparedness
- Personnel Safety
- Environmental Protection
Each category is weighted as to its’ relative risk importance and a target facility risk rating is determined. Then using the following risk levels in Table 1, the facility is evaluated.
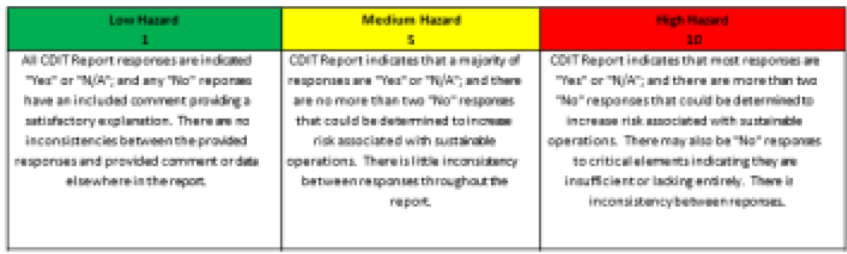
Each category is then assigned to one of the four described dimensions and each dimension is assigned a relative percentage according to Table 2 below.
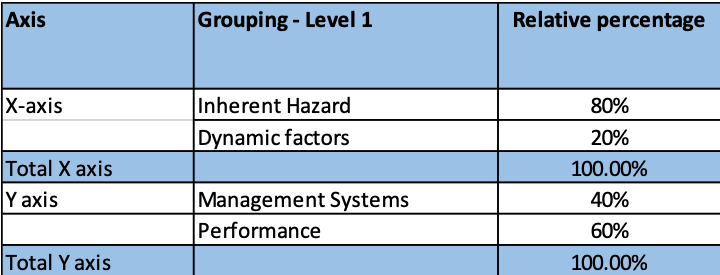
Finally, a terminal overall risk score is determined. The score is shown on a chart that can be tailored to each client’s risk acceptance profile.
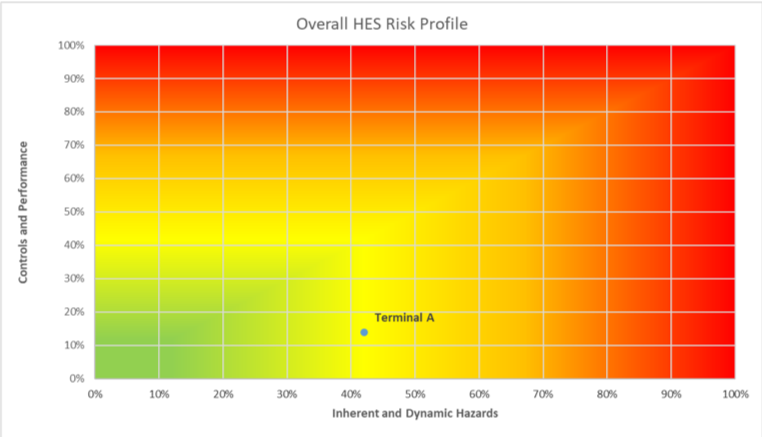
Each client can then determine their trigger point for conducting on-site audits. The results of the CDI-T report evaluation can be used to focus the audit reducing time and cost. A typical 4-5 days on-site audit can be reduced to 1-2 days.
This process delivers a meaningful metric based on specific client risk tolerance that can be used to communicate with management and justify additional auditing resources as needed. Additionally, the process can be used as a tool to help select storage terminals when negotiating new business arrangements.
For more information on the storage terminal risk assessment process, please visit TKC Global Consulting at TKCGlobalConsulting.com or contact Ted Caudill, PE at ted@tkcglobalconsulting.com or 713-516-2864 (USA).